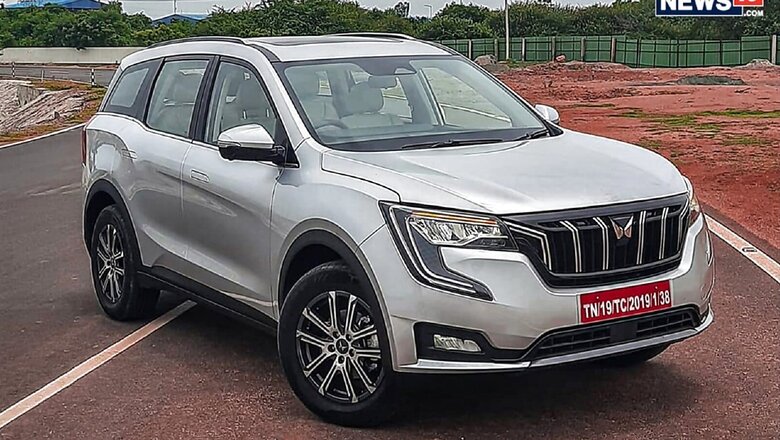
views
The upcoming Mahindra XUV 700 is one of the most awaited cars launches of 2021. This latest Mahindra offering is expected to spice up the competition in the SUV segment in India and if its feature list is any hint, the product could be a nightmare for its competitors. Now, while the feature offering list of the XUV700 is long and impressive, one aspect where the company will have to perform well is the safety measurement. Buyers today take the safety offering of cars very seriously and Mahindra knows it. The company's earlier launch XUV 300 scored well at the NCAP rating and is currently the safest made in India car with the highest Global NCAP safety rating. Mahindra would be expecting to repeat this performance and is all geared up with the XUV 700.
Mahindra XUV 700 Safety Features
While Mahindra XUV 700 is yet to take the NCAP crash test, its safety features give a hope ofgood rating. The upcoming SUV has been equipped with a series of modern features that include seven airbags, a rear parking sensor, a rear parking camera, ABS with EBD and an ADAS (Advanced Driver Assitant System), among many other offerings that will ensure the safety of the passengers on board, reported on Rushlane. The features sound impressive but what about the strength of the car's structure? Youtuber Motor Vikatan talked about the safety of the XUV 700 in his recent uploads and explained the process of development of the SUV's safety.
Stimulation Phase
The initial stage of the developmenthas stimulation of various types of crashes that helps the developers to build a more crash-resistant setup. First, the front end of the car is analysed to see how well it can absorb the impact of a crash.
In the case of XUV 700, the front end, much like the other parts of the monocoque frame underpinning, has been made with the use of high strength steel. Hence, the impact of the crash in absorbed deforming the engine bay and distributethe resultant load in a systematic manner that it doesn't cause any intrusion to the front compartment or hard occupants.
Similarly, for the side impact stimulation, intrusion resistant materials are used in the side panel and the airbags further enhance protection. For impact on the read end, long member and cross member absorb the impact energy. The long member placed at the rear bumper absorbs the crash shock and stop it from reaching the fuel tank.
Also Watch:
The overall stimulation phase takes about 8 to 9 months of development going through checks. Companies also take special care that the rear suspension doesn't intrude fuel tank which in case of accidents could cause fire hazards.
Testing Phase
After completion of the stimulation process, a prototype is created and testing begins. Meanwhile, the company also analyse the difference between the results of the virtual stimulation test with the real-life test and evaluate the performances.
Read all the Latest News, Breaking News and Assembly Elections Live Updates here.
Comments
0 comment